Dal luglio 2018 (sentenza TAR Lombardia) a fine settembre dello stesso anno è esplosa la questione fanghi che ha fatto temere il blocco dei depuratori delle acque fognarie dovuta al periodo di sospensione temporanea per lo smaltimento nell’ambito agricolo. Da allora abbiamo avuto interventi e prese di posizione da parte di Regioni, T.A.R, Corte di Cassazione, Provincie, Governo, con ordinanze e sentenze che hanno evitato di fermare gli impianti perché le conseguenze sarebbero state catastrofiche considerando che uno dei canali di smaltimento sul terreno agricolo ne rappresenta la principale modalità con circa il 38 percento.
Le difficoltà di smaltimento di questi ultimi anni hanno però influito in maniera pesante sul prezzo di smaltimento dei fanghi che da 40-50 euro/ton è aumentato a 180-250 euro/ton in funzione del tipo di fango e delle zone geografiche in cui sono collocate le varie aziende.
Considerando tale aumento di costi, le aziende hanno e stanno installando una serie di attrezzature che permettono di ridurre il peso dei fanghi prodotti e destinati allo smaltimento.
In primo luogo hanno installato sistemi di disidratazione meccanica quali centrifughe o nastro presse che consentono, meccanicamente, di aumentare la sostanza secca del fango fino al 22-25 percento, che è il limite massimo ottenibile dai sistemi meccanici.
Per aumentare oltre la sostanza secca si deve poi ricorrere ad altri sistemi fra cui l’essiccazione, che permette di ottenere una sostanza secca fino al 90-95 percento.
In tale ambito rientrano gli impianti di essiccazione progettati e realizzati da Scolari, proposti con capacità evaporative differenziate e possono soddisfare le esigenze di piccole, medie e grandi aziende e comunità civili.
La tecnologia applicata è quella con tappeti forati sovrapposti che assicurano l’essiccazione del fango in maniera uniforme e omogenea. Gli impianti sono realizzati in Aisi 304, con quadro elettrico che gestisce in automatico l’impianto e il sistema, ad umido, per il trattamento dell’aria satura in uscita, che assicura il rispetto dei limiti regionali previsti per le emissioni.
Utilizzano bassa temperatura, può variare dai 78 ai 150 °C, in funzione della termica disponibile in azienda che può essere ottenuta da acqua calda, fumi di scarico, vapore, acqua surriscaldata o da combustibili fossili come gas naturale o GPL.
Scolari ha realizzato i primi impianti di essiccazione fanghi in Austria e alcuni impianti per fanghi industriali in Italia, negli anni 70. Settore che non ha avuto sviluppo, all’epoca, per i limitati costi di smaltimento che erano nell’ordine di 10-15 euro/ton.
Nell’ultimo periodo Scolari ha realizzato decine di impianti nel settore depuratori civili, industriali, agroindustriali, ambientale.
I cicli di lavoro degli impianti possono essere in continuo o alternativi, in funzione della disponibilità della termica e delle esigenze aziendali.
In generale quando la termica è disponibile h24, l’impianto è utilizzato 8.000-8500 ore/anno; mentre, quando si utilizza gas naturale o biogas esso lo si impiega, normalmente, con gli stessi turni di lavoro aziendali che possono essere h24 o 16/24 ore.
L’utilizzo degli impianti a ciclo continuo o intermittente non comporta perdite di rendimento termico nè tempi morti per l’entrata a regime quando si riparte con la lavorazione.
La progettazione e la realizzazione è fatta in funzione delle esigenze specifiche del cliente e può essere: con condensazione e riciclo dell’aria satura in uscita dal camino, recupero termico con sistema di preriscaldo dell’aria ambiente in ingresso all’impianto, sottraendo parte del calore (sia sensibile sia latente di condensazione) al flusso d’aria satura in uscita dall’essiccatoio con riduzione dei costi di esercizio valutabile nell’ordine del 15-20 percento. Trattamento a umido con doppia torre di lavaggio e, se necessario, biofiltro.
Gli impianti sono normalmente realizzati con un unico gruppo generatore di calore e unico sistema di aspirazione collegato con torri di lavaggio dell’aria satura in uscita che, con un solo camino di scarico in atmosfera, semplifica la domanda autorizzativa per l’installazione.
La gestione di tutte le componenti dell’impianto (essiccatoio, gruppo generatore di calore, scrubber o biofiltro) è prevista tramite un’unica interfaccia (pannello operatore) sul quadro di comando generale, così da facilitarne enormemente la conduzione da parte dell’operatore.
La progettazione è dettagliata e particolarmente curata con accorgimenti specifici per garantire la massima sicurezza attiva e passiva durante l’uso e la manutenzione.
Il rendimento termico è ottimizzato grazie all’isolamento termico delle pareti laterali dell’impianto, che riduce al minimo la dispersione termica oltre al riutilizzo dell’aria calda di essiccazione che, in uscita dal tappeto inferiore, preriscalda il prodotto umido in entrata sul tappeto superiore.
IL ciclo dell’aria di processo è ottenuto con ventilatori di mandata e di aspirazione controllati da inverter e pressostato per garantire l’interno dell’impianto in depressione ed eliminare fuoriuscite di polveri e odori e/o percorsi preferenziali dell’aria.
Il processo di essiccazione, normalmente, permette di ridurre il peso del materiale in funzione dell’umidità iniziale e finale. Nella maggior parte dei casi i fanghi umidi sono centrifugati o nastro pressati e hanno una sostanza secca del 22 percento.
Essiccandoli al 15 percento di umidità finale (sostanza secca 85 percento) abbiamo una riduzione di peso del 70 percento, e ciò significa che da 1.000 kg di umido ne rimangono 300 kg di secco.
Il costo di essiccazione corrispondente, per l’essiccazione di 1 ton di umido, riferito al gas naturale, può essere valutato, verosimilmente, nell’ordine di 25 euro. Il minor costo di smaltimento, sommato al costo di essiccazione, dovuto al minor peso del materiale da conferire in discarica, con costo di smaltimento considerato di 200 euro/ton, risulta di 90 euro/ton.
Pertanto, anche qualora, non vi sia la possibilità di recuperare termica a costi zero e si dovessero utilizzare combustibili tradizionali (metano o GPL) abbiamo che il minor costo di smaltimento del fango essiccato rispetto a quello del fango tal quale, inclusi i costi di esercizio, si può verosimilmente indicare nell’ordine del 50 percento.
Minor costo che può raggiungere circa il 70-75 percento quando vi è la possibilità di recuperare termica disponibile in azienda, a costo zero.
Nella valutazione precedente si sono considerati i soli costi d’esercizio e non quelli di ammortamento, strettamente condizionati dalle condizioni di lavoro dell’impianto (ore lavorative annue, capacità produttiva, ecc.).
In condizioni normali, se gli impianti sono proporzionati alle esigenze aziendali e lavorano 6-8.000 ore/anno, il rientro del capitale investito può essere considerato nell’ordine di 1,5-2 anni di utilizzo.
Gli impianti Scolari rispettano le caratteristiche tecnico-scientifiche previste nel quadro del piano europeo denominato “Industria 4.0” e in Economia Circolare, e questo permette di usufruire degli incentivi previsti per questa tipologia di impianti e ridurre in maniera significativa i tempi di ammortamento. Inoltre, se i fanghi non contengono metalli pesanti e possono essere recuperati per ripristino ambientali o per altri utilizzi, si elimina anche il costo dello smaltimento.
L’essiccamento dei fanghi a bassa temperatura
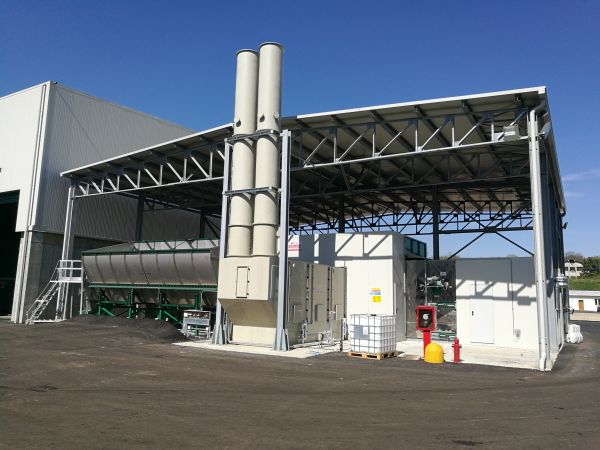